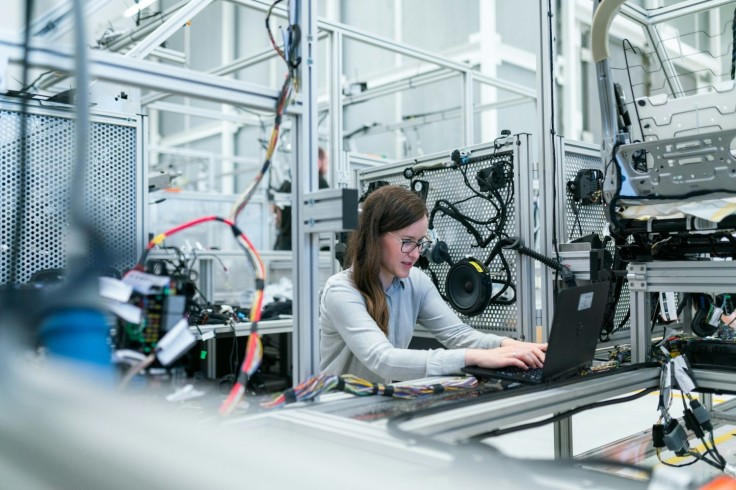
After the collapse of manufacturing capacity in most developed economies from the 1980s to the early 2000s, these countries have leaned heavily on globalized supply chains. These chains are vulnerable. For example, when the Suez Canal was obstructed in 2021 by the Ever Given container ship, the supply chains were hugely disrupted, blocking the import of many goods that would previously be manufactured internally. Such disruptions and the growing tensions among members of the international community have led to a push for more onshore manufacturing. The question is, who will develop the manufacturing capacity, and how will they do it?
Certain entrepreneurial individuals, both independently and within established companies, will be the ones to take up the slack in onshore manufacturing. But this leaves the latter question unanswered: will they embrace the philosophy of lean manufacturing? This article will delve into this question and ultimately answer it in the affirmative.
The Philosophy of Lean Manufacturing
There are numerous manufacturing philosophies, but the one that has gained traction recently, enough so to warrant a master's degree in lean manufacturing, is, as the degree title would suggest, "lean manufacturing." Ultimately, lean manufacturing boils down to the attempt to leave nothing to waste. To achieve this, the philosophy embraces five principles:
1. Defining Value
This involves identifying and optimizing what customers consider valuable. Anything that doesn't add value to the end product is seen as waste.
2. Mapping the Value Stream
This step requires companies to analyze their production process to identify and eliminate waste.
3. Creating Flow
The goal here is to ensure that production steps run smoothly without interruptions, delays, or bottlenecks.
4. Establishing Pull
Instead of producing goods in advance and pushing them to the market, lean manufacturing relies on customer demand to pull products through the production process.
5. Pursuing Perfection
Continuous improvement is a core tenet of lean manufacturing. Companies must strive for perfection by consistently removing waste and improving processes. In a word, optimize.
The Benefits of Lean Manufacturing
There are two categories of benefits to lean manufacturing. Firstly, the internal benefits to the competitiveness and overall success of companies who embrace the philosophy. Secondly, the external benefits of the greater society and the world, given a widespread embrace of lean manufacturing.
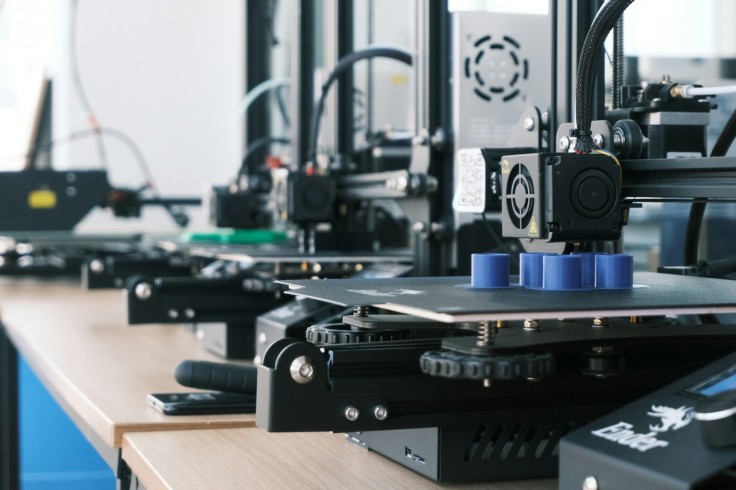
Efficiency and optimization are at the core of lean manufacturing, driving significant internal benefits for companies. By streamlining production processes, reducing cycle times, and eliminating waste, organizations can operate more smoothly and predictably. This optimization process can directly be measured in cost reduction. Avoidable costs are reduced directly in proportion to the leaner the company can stably maintain. Moreover, improved efficiency can lead to increased production capacity without the need for additional resources, allowing companies to scale more effectively. These cost savings will allow for a greater production capacity for the company. Lower costs and greater production are the formula for success.
Beyond the internal advantages, lean manufacturing can have a profound positive impact on the world. By minimizing waste to as close to zero as possible, the companies will minimize their reliance on fossil fuels to only that which is necessary for production. Furthermore, lean manufacturing's focus on quality and efficiency can lead to safer, more reliable products, benefiting consumers and society at large. Thus, lean manufacturing benefits the environment in the form of reduced carbon emissions and benefits society in the form of higher-quality products.
Will Lean Manufacturing Be Embraced?
Yes. Lean manufacturing will be embraced as the guiding philosophy for the growing manufacturing sector. The reasons for this are simple. Our economy follows a competitive market structure. Companies that have a higher production capacity and lower running costs will out-compete suboptimal companies. Lean manufacturing is the process by which companies most successfully optimize their manufacturing process. As such, only those companies that embrace this philosophy will succeed in a competitive market.
The efficiency gains, cost reductions, and quality improvements inherent in lean manufacturing make it not just an attractive option but a necessary one for survival and growth in today's volatile economic landscape.
Conclusion

In conclusion, lean manufacturing represents a transformative approach that aligns with the needs of modern manufacturing. The internal benefits of efficiency, cost reduction, and quality improvement, coupled with the external benefits of environmental sustainability and societal advancement, make it an indispensable strategy.
As global supply chains face increasing vulnerabilities, the shift toward onshore manufacturing underscores the necessity for lean principles. Companies that embrace lean manufacturing will be well-positioned to thrive, setting new standards for efficiency and sustainability. The future of manufacturing, guided by lean principles, promises a more resilient, competitive, and responsible industrial landscape.
Lean manufacturing will also appeal to the upcoming class of leaders who are driven to build successful companies that generate a positive impact on the world. Lean manufacturing has both the force of market competition and the human drive for success on its side.