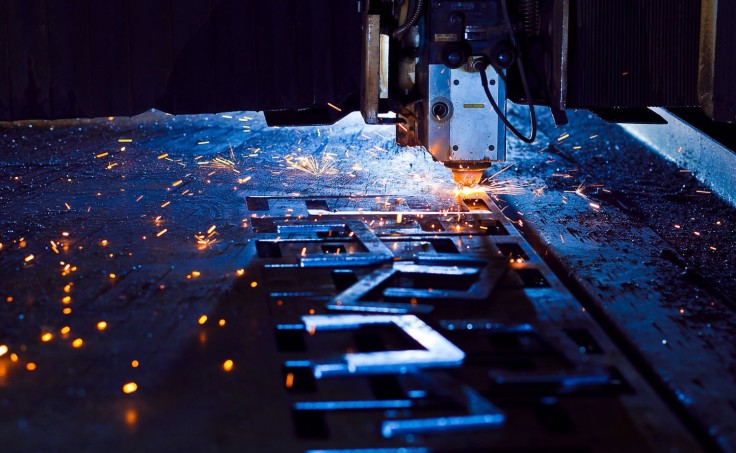
What is sheet metal?
Sheet metal is simply metal that comes in sheets. While sheet metal comes in different gauges of thickness, it is thinner than plate metal but thicker than foil. Steel and aluminum are the most common metals that are available in this form and there are various coatings and for corrosion resistance and surface finishing. Sheet metal is a very versatile material for producing prototypes and finished products in many different industries. From airplanes to air conditioners and from soda cans to car parts, sheet metal is vital to the production of many things.
There are specific industries and products that use sheet metal and others where it is not as effective. For small parts where complex or precise geometry is needed, sheet metal is not ideal. Likewise for lightweight products, highly cosmetic finishes, and high volume orders, another type of material should be found. On the other hand, for large and durable parts with few features, sheet metal is ideal. It is also great for thicker parts and for adding strength and weight to other products.
A sheet metal fabrication service will always begin with a single, blank sheet of metal. The process of forming this blank piece of sheet metal is by cutting, punching, or bending the metal to the desired design specifications. You do not add anything to the initial material, you simply form the raw material into the design that you desire. Only after the design is complete do you add finishing touches like paint or corrosion finish.
How are sheet metal parts made?
While low volume orders are a better fit for sheet metal production, high volume orders can be handled as well. There is a slight difference in how high volume orders are produced compared to low volume orders, but the following will give you an idea of how sheet metal parts are made.
Low Volume
At low volumes, a sheet metal fabrication service will use one of three possible techniques: punching, lasering, or bending. The technique used depends on the complexity and nature of the design being created.
The punching technique is very similar to using a hole-punch on a sheet of paper. Holes are punched either for cosmetics or so that a screw can be attached to connect one thing to another. Laser cutting is exactly what it sounds like. A highly concentrated laser is used to cut when bigger and more exact cuts than punching can handle are necessary. Bending is the last technique used and is important when designing sheet metal. A hydraulic press is used to bend the metal to the desired specification. This is by far the most expensive design technique because there must be a human operator present for each bend.
High Volume
High volume sheet metal orders, on the other hand, will almost always use stamping to produce the finished product. A stamping tool is generally expensive and designed for a single purpose making it very cost-ineffective. However, for high volume production of 1,000 parts or more, stamping is worth it.
For these high volume jobs, a process called progressive die stamping is used. Two large pieces of metal with multiple punching tools are placed above and below the sheet metal being designed. These stamping tools are set to punch the sheet metal at the exact right places with one movement forming the sheet metal to the specifications provided. It is good for high volume jobs because it can do this over and over-producing the desired result quickly and efficiently.
What is sheet metal used for?
Punched Features
The direction and length of the punch are very important for punched features. If the punching tool is not long enough, it will not punch the metal completely. If the punch is done in the wrong direction then the finishing touches will not look right compared to the rest of the job. Other than for design and aesthetics, the most commonly used punch feature is a "screw boss" function that can accept self-tapping screws that can be added later.
Bend Features
Though bending is the most expensive of the design features, it is also what gives shape and strength to a product. Some of the features of bending include:
Jog bends which is the technique of putting two bends together.
Hand bends are when a line is punched so that a person can bend it later.
Hems are created when an end of the sheet metal is bent back against itself.
Cross breaks are large bends that add a little height to a project and stiffens it to fight against buckling.
Learn how to select the right manufacturing process for your metal parts. Easily compare CNC machining and additive manufacturing (AM) technologies online.