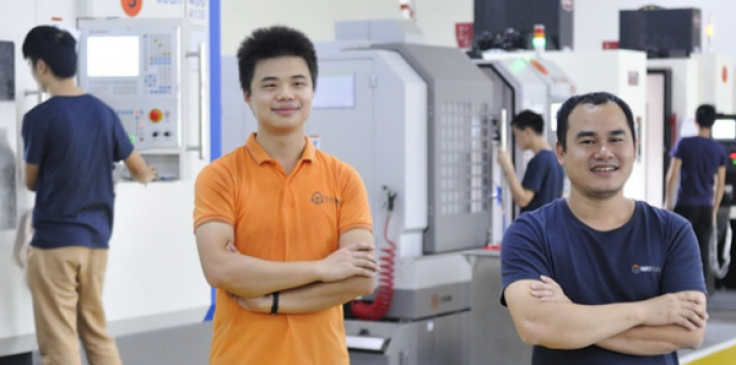
Cars are unique products in a number of ways. Usually, when we choose a device, we look at its specifications: what can it do, how many features it has, how big it is, etc. But when we choose a car, aesthetics is often more important than its maximum speed, acceleration rate, or clearance. This led to automotive vehicles becoming a work of art. Modern cars can boast elegant and beautiful designs, complex forms, and a lot of accessories. Creating such elements poses a real challenge to the engineers and manufacturers. Doubly so for the automotive lighting parts. Not only do they have to be complex and elegant, but they must also be either crystal clear or mirror-like to produce the desired lighting.
Why Automotive Lighting Production Requires High Competence
So, it's even harder to design and manufacture car light elements due to their specific requirements: either mirror-like or optical clear surface finish. Let's see, why it is so hard to produce car lenses or reflectors and why it is extremely important to hire specialists to do it.
Automotive lighting prototypes require a lot of equipment. The lenses are usually made of polymers (PC or PMMA) and require special equipment and tooling to cast. The first task of a lighting prototype manufacturer is to make specific tooling that will produce high-quality plastic parts for further processing. After the initial casting follows a step by step process of getting to the right surface finish. First comes CNC machining, then a lot of manual polishing operations, and with each step, the price of error gets higher because of the time and effort put into the part.
Ways to Ensure The Desired Result
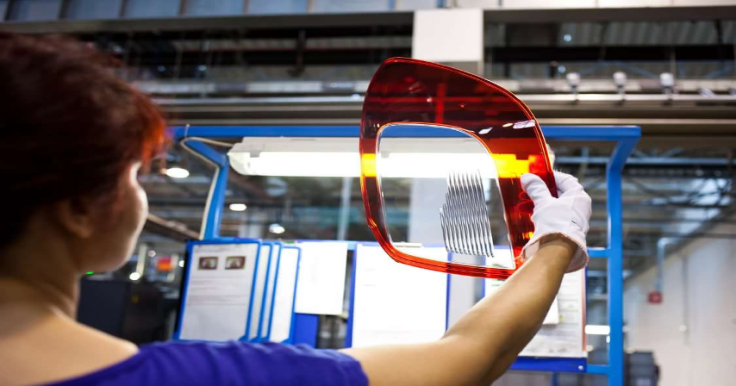
Professional prototype manufacturers have some ways to ensure that the car lenses are going the right way from blanks to high-quality automotive parts with a number of tools and methods:
● CNC machining with 6 degrees of freedom. The best surface can be achieved with a ball nose end mill, high speed, low feed rate, and keeping the tool axis normal to the machined surface. Complex organic car light surfaces require more degrees of freedom and so the best prototype manufacturers employ 5-axis CNC machine tools that can keep the tool oriented in any direction during the cut.
● Wise part separation. Some complex parts are just too hard to manufacture. In order to make the job easier, manufacturers split one part into simpler elements and bind them together. Wise part separation and binding material choice play a large role in the ability to produce the desired prototype fast.
● Two-component molding techniques. Some of the automotive light elements consist of multiple plastic types welded together. This requirement is easily achieved with 2k molding. You can mold a second plastic over a complete part when it still cools down and solidifies. However, this technique is very specific and you just won't have the equipment for it if you don't do plastic manufacturing regularly.
● High profile hand polishing experts. Mirror-like and optically clear surface finish is not achieved easily. You have to grind down from rough sanding paper up to the finest paste. It takes time and a lot of skill to polish a car lens to the required clarity. Polishing experts are very valuable and expensive in the automotive market and high-grade machine shops like to keep the best.
High-Precision Machining of Car Lighting Parts
In order to decrease car light prototype production time and the time of manual labor, advanced manufacturers employ 5-axis high-precision machine tools that can process materials with tolerances close to 0.05 mm. But apart from that, you can use special expensive cutting mills. Diamond single-point mills can significantly decrease the amount of manual polishing required for the production of optically clear parts. Diamond milling is often called optical machining for its specialized use in the manufacturing industry.
Typical Automotive Lens Types
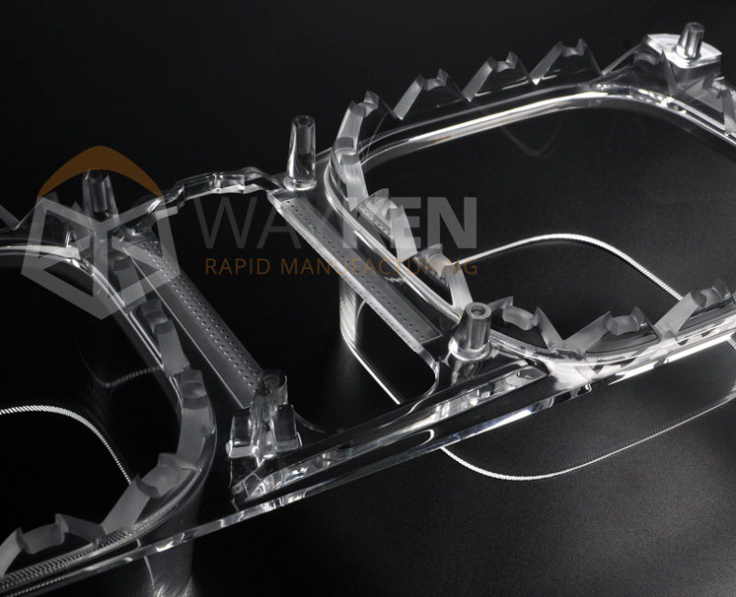
There are 3 main types of automotive lens: Lamp bezel, light guides, and light blades. Lamp bezels and light blades are considerably easy despite having complex surfaces. However, light guides are long hollow polycarbonate tubes that are quite hard to process. You have to split them up, CNC machine them separately from each other, and then join the pieces back together. The cost of a mistake is very high with those parts.
Making Lighting Reflector Prototypes
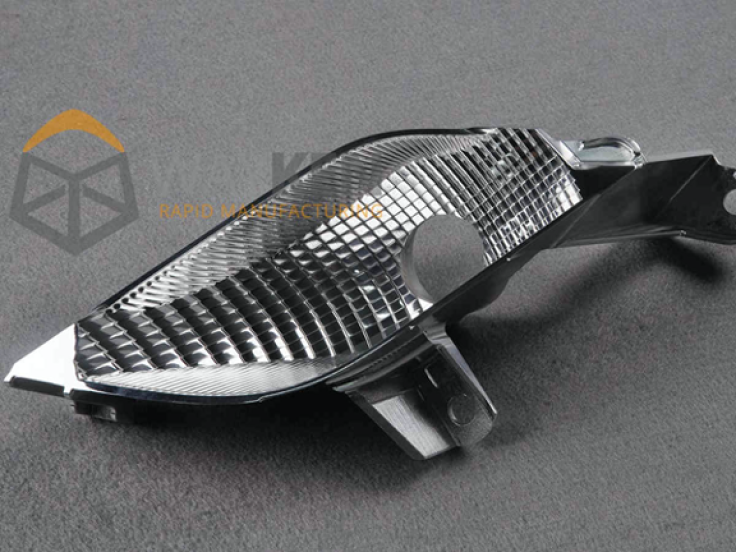
Lighting reflectors are the parts that ensure all the light emitted from the bulb goes in the desired direction. They are usually made of metal (aluminum alloys are the most widespread type) and then processed to have a mirror-like surface finish along its front surfaces. The quality of the surface is a staggering Ra 0,2 mcm. And that is to say that the reflector has complex surfaces. In order to process them, high speed, high-efficiency 5-axis milling processes are developed. After that, a person uses sanding paper and special abrasive pastes to polish the surface to a perfect condition. Apart from the surface finish, the part must maintain constant curvature, otherwise, you risk the light from the bulb spreading unevenly and ruining the lamp.
Achieving the Next Step From Prototype And Small Batch Production of Car Lights To Mass Manufacturing
Automotive lamp prototypes are usually made with a combination of silicone casting, CNC machining, and hand polishing. However, what if the design turned out to be successful? You will have to move on to the next step. And this next step includes injection molding, which requires complex tooling to be made fast, and ways to polish PC efficiently. This includes vapor polishing. It is a process that uses very specific equipment.
What I am trying to say is that it is best to leave automotive light production (prototype or mass) to a very capable team. Outsourcing is a great way to cut the losses that inevitably appear when your production does not specialize in automotive optical prototyping.
Conclusion
AutoProtoWay.com is a new subwebsite of Wayken Rapid, which is focusing on complete automotive lighting prototypes service for the customers around the global.
In our machine shop, we can offer precision machining of optical components such as lamp bezel, light guide and light blades etc with advanced 5-CNC machines. If you want to understand us more, please don't hestitate to contact with us: AutoProtoWay@waykenrm.com or Tel: +86 755 2373 1920.