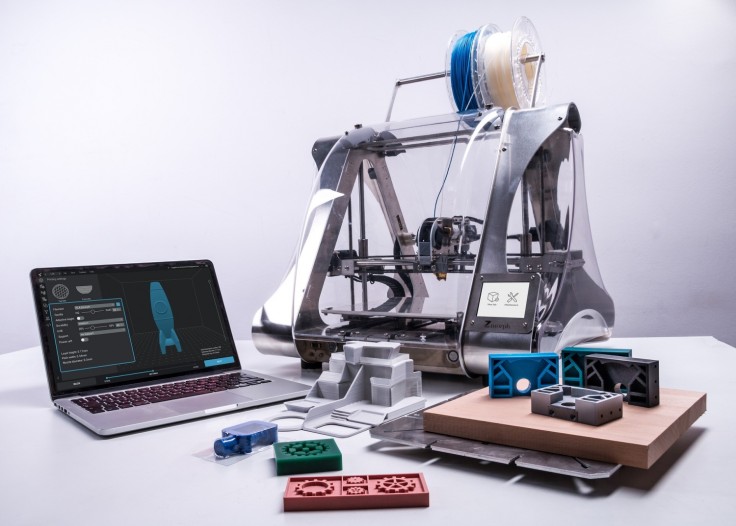
The process of prototyping and creating new components through 3D printing is limited by a number of factors; the materials and the process. Until now, the most popular material for 3D printing has always been thermoplastic elastomer or TPE. However, this is typically a soft material which makes it difficult to manage in the 3D printing process. Protolabs has developed a new material which addresses the concerns of TPE printing and offers new possibilities for creating ever more intricate, delicate and precise components.
UltrasintTM TPU01 is a thermoplastic polyurethane (TPU) which lands somewhere between a rubber and a plastic. This means that it has rubber-like tendencies, but also offers incredible durability. It's highly resistant to abrasion, oil, grease and UV. It's also more rigid than TPE and therefore less likely to shrink.
3D printing with TPU typically involves selective laser sintering (SLS) or fused deposition modelling (FDM) but these methods are limited in their own ways. By adding multi-jet fusion with TPU to the list, Protolabs has opened up a world of design possibilities.
What is multi-jet fusion 3D printing?
Multi-jet fusion is a 3D printing process that uses an inkjet array to apply fusing and detailing agents to a bed of powder. After each layer is complete, a new layer of powder is added on top and the process repeated until the component is complete. After this, any leftover powder is removed using a vacuum and then the parts are bead blasted to remove any residue. Finally, the part is dyed black to improve its appearance. It is an incredibly fast process which is perfect for rapid prototyping or for creating a finished product.
Ideal for prototyping and production
When developing products, designers will typically cycle through a rapid prototyping process before landing on a final design and going into mass production. With multi-jet fusion, the same process can be used to create the prototype as is used to create the finished product. Once the design is finalised, multi-jet fusion can be just as easily employed for mass production. The process can produce components with incredibly precise parameters without sacrificing strength and durability.
Possibilities of UltrasintTM TPU01
It should come as no surprise that TPU can be used to create a range of components. The rubber-like nature of the material lends itself to parts that need to be elastic, durable or shock-absorbing. This makes it perfect for sports and leisure applications, including running shoes and hoses. As it is also chemical and oil resistant with good thermal resistance, it can also be used to create lightweight and durable parts for cars and other transportation. It can be used to create ducts, seals and gaskets to a range of specifications. Perhaps the biggest advantage of UltrasintTM TPU01 is that it can be used to create anything for a comparatively low cost.
Precision engineering of parts
For those interested in the technical aspect, you might be interested to learn the specifics of this material and this 3D printing process. This material can achieve tolerances of +/- 0.30mm and 0.002mm/mm on well-designed parts. UltrasintTM TPU01 has a shore hardness of 88A and a tensile strength of 9MPa +/- 2MPa on the x-y plane. And it has an elongation at break greater than 220%.
This is all great news when tasked with creating components which need to be precision engineered. And if you don't have the engineering capabilities in-house, Protolabs will make their design team available to you. This means you can conceptualise, design, prototype and produce your components all under the same roof, ensuring that no part in the production process is overlooked.